不锈钢加工难点主要有以下几个方面:
The difficulties in stainless steel processing mainly include the following aspects:
1. 切削力大,切削温度高
1. Large cutting force and high cutting temperature
该类型材料强度大,切削时切向应力大、塑性变形大,因而切削力大。此外材料导热性极差,造成切削温度升高,且高温往往集中在刀具刃口附近的狭长区域内,从而加快了刀具的磨损。
This type of material has high strength, large tangential stress and plastic deformation, so it has high cutting force. In addition, the poor thermal conductivity of the material results in the increase of cutting temperature, and the high temperature is often concentrated in the narrow and long area near the cutting edge, thus speeding up the wear of the tool.
2. 加工硬化严重
2. Severe work hardening
奥氏体不锈钢以及一些高温合金不锈钢均为奥氏体组织,切削时加工硬化倾向大,通常是普通碳素钢的数倍,刀具在加工硬化区域内切削,使刀具寿命缩短。
Austenitic stainless steel and some high-temperature alloy stainless steel are austenitic structure, and the working hardening tendency is large when cutting, which is usually several times of that of ordinary carbon steel. The tool cutting in the working hardening area shortens the tool life.
3. 容易粘刀
3. Easy to stick knife
无论是奥氏体不锈钢还是马氏体不锈钢均存在加工时切屑强韧、切削温度很高的特点。当强韧的切屑流经前刀面时,将产生粘结、熔焊等粘刀现象,影响加工零件表面粗糙度。
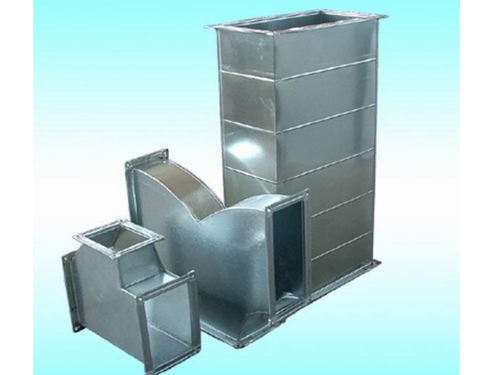
Both austenitic stainless steel and martensitic stainless steel have the characteristics of chip strength, toughness and high cutting temperature. When the strong chips flow through the front cutter face, there will be adhesion, fusion welding and other phenomena, which will affect the surface roughness of machined parts.
4. 刀具磨损加快
4. Accelerated tool wear
上述材料一般含高熔点元素、塑性大,切削温度高,使刀具磨损加快,磨刀、换刀频繁,从而影响了生产效率,提高了刀具使用成本。
The above materials generally contain high melting point elements, large plasticity and high cutting temperature, which make the tool wear faster, and the tool grinding and changing are frequent, thus affecting the production efficiency and increasing the use cost of the tool.
主要是降低切削线速度,进给。采用专门加工不锈钢或者高温合金的刀具,钻孔攻丝更好内冷。
It is mainly to reduce the cutting line speed and feed. Special cutting tools for stainless steel or superalloy are used, and internal cooling is best for drilling and tapping.
上一篇:选用玻璃钢通风管道有什么要求!
下一篇:玻璃钢管道未来的发展前景